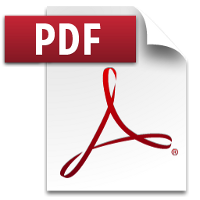
R 385.00
Occupational Health and Safety Act, 1993 (Act No. 85 of 1993)Code of PracticeDiving Regulations, 2009Code of Practice for Inshore Diving6. Task related equipment |
6.1.1 | High-pressure water jetting and LP abrasive cleaning |
Even an apparently minor accident with this equipment has the potential to cause a serious internal injury to the diver. A dive plan that includes the use of such units will therefore also need to include safe operating procedures that will need to be followed.
6.1.2 | Lift bags |
The use of lift bags under water can be hazardous. The dive plan will need to include ways to prevent the uncontrolled ascent of a load. Good practice established by the industry will need to be followed.
6.1.3 Abrasive cuffing discs
The dive plan will need to address the risk of abrasive cutting discs breaking during use under water. In particular, the adhesive used in these discs tends to degrade in water. The plan will need to ensure that only dry discs not previously exposed to water are used, and that only enough discs for each dive are taken under water at any one time.
6.1.4 | Oxy-arc cutting and burning operations |
There are inherent hazards in the use of oxy-arc cutting and burning techniques under water, including explosions from trapped gases trapping of divers by items after cutting, etc. Guidance on this subject exists. The dive plan will need to include precise instructions regarding the operating procedures. Procedures which eliminate blowback, etc. will need to be employed.
6.1.5 | Equipment - General |
6.1.5.1 | Equipment register |
An equipment register should be maintained at the worksite with copies of all relevant certificates of examination and test. It should contain any relevant additional information, such as details of the materials used to construct diving bells and surface compression chambers. lt should also contain details of any applicable design limitations, for example, maximum weather conditions for use, if applicable.
6.1.5.2 | Suitability of equipment |
The diving contractor will need to be satisfied that the equipment provided for the diving project is suitable for the use to which it will be put, in all reasonably foreseeable circumstances on that project. Suitability can be assessed by means of evaluation by a competent person, clear instructions or statements from the manufacturer or supplier, physical testing, or previous use in similar circumstances.
New, or innovative equipment must be considered for safety and fitness for purpose, but should not be discounted only because it has not been used before. Single-point failure consequences, both for the equipment components and for operating procedures, must be considered in the HIRA.
6.1.5.3 | Certification of equipment |
The standards and codes used to examine, test and certify plant and equipment, and the requirements of those who are competent to carry out such examinations, tests and certification, must be followed. Suitable certificates (or copies) will need to be provided at the worksite for inspection.
6.1.5.4 | Maintenance and testing of diving equipment |
Diving plant and equipment is used under extreme conditions, including frequent immersion in salt water. It therefore requires regular inspection, maintenance and testing to ensure it is fit for use, e.g. that it is not damaged or suffering from deterioration.
6.1.5.4.1 | Períodic examination, testing and certification |
Detailed guidance exists (Specific regulations, SANS codes, IMCA codes, manufacturer's guidelines, etc.) on the frequency and extent of inspection and testing required of all items of equipment used in a diving project, together with the levels of competence required of those carrying out the work.
6.1.5.4.2 | Planned maintenance system |
The diving contractor must establish a system of planned maintenance for plant and equipment.
Such a system may be based on either passage of time or amount of use, but ideally will be based on a combination of both. For each major unit, the system should identify the frequency with which each task is to be undertaken and who should do the maintenance work. The responsible technician will then need to provide and file a record of the maintenance work.
6.1.5.4.3 | Maintenance of cylinders used underwater |
Diverse emergency gas supply cylinders (bail-out bottles) and cylinders used underwater for back-up supplies on diving bells and baskets can suffer from accelerated corrosion. Particular care will need to be taken to ensure that they are regularly examined and maintained. Cylinders used underwater should be tested in accordance with the requirements for Scuba cylinders as detailed in SANS 10019, and should be internally inspected for the presence of water if there is sufficient reason to suspect such contamination.
6.1.5.4.4 | Lifting equipment design, periodic test and examination requirements |
All lifting gear, such as sheaves, rings, shackles and pins should have test certificates when supplied and be examined at six monthly intervals thereafter. The certificates should show the SWL and the results of load tests undertaken on the components to 2 x SWL.
6.1.5.4.5 | Maintenance of bell and basket lift wires |
Frequent immersion in salt water, shock loading from waves, passing over multiple sheaves, etc, can cause wear and deterioration to the lift wires of diving bells and baskets if they are not properly maintained. Specialised advice on maintenance exists, and will need to be followed to ensure that wires remain fit for purpose.
6.1.5.4.6 | Maintenance of lift bags |
Manufacturers' maintenance instructions and testing requirements will need to be followed.
6.1.5.4.7 | Maintenance and testing of chambers |
Details regarding the maintenance and testing of chambers is contained in other Regulations under the Act.
6.1.5.4.8 | Testing immediately before use |
All diving equipment used must be checked and tested by the dive team before use so as to determine whether it is in good working order.
6.1.5.4.9 | Additional diver's equipment requirements |
In addition to the required working equipment of the divers, the following accessories and equipment must also be provided:
• | diver's location indicator devices, e.g., rescue beacons or strobes, where SCUBA diving operations are to be carried out during the hours of darkness; and |
• | a dive knife. |
• | a diving harness, complete with lifting ring, worn by each diver. |
Immediately before each dive, the diver shall check that all his required equipment is present; such equipment is properly fastened in place; and all his apparatus is functioning properly. Before descent, the same check shall be conducted in the water.
6.1.5.4.10 | Surface control point equipment |
When diving is in progress, a surface control point shall be equipped, as a minimum, with the following equipment:
• | if SCUBA is being used, then one complete spare set of underwater breathing apparatus with fully charged cylinders for emergency purposes; |
• | one weighted shotline, of sufficient length to reach the bottom at the maximum depth of the work area; |
• | a first-aid kit appropriate for the size of the work crew and work location; |
• | one set of decompression tables, appropriate for the depth range and breathing gas in use; |
• | therapeutic oxygen and administration equipment; |
• | an adequate two-way communication system connecting the dive site with medical assistance; |
• | adequate means to facilitate the entry and exit of divers to and from the water; |
• | adequate means to facilitate the immediate removal from the water of an unconscious diver; |
• | such other equipment as may be needed to ensure safe operations. |