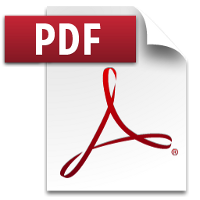
R
Occupational Health and Safety Act, 1993 (Act No. 85 of 1993)Code of PracticeNational Code of Practice for Electrical Machinery in Hazardous LocationsRegulatory requirements for explosion-protected apparatusAnnexesAnnex D (normative) : Minimum requirements for certification of second-hand Ex equipment without an IA certificate |
Annex D
(normative)
Minimum requirements for certification of second-hand Ex equipment without an IA certificate
D.1 | General |
D.1.1 | A checklist shall be compiled by the responsible ATL and results shall be recorded. The checklist shall cover the requirements of the protection technique and shall be based on the current or previous version of the applicable Ex standard. |
The checklist may also be used as the basis for a repair checklist.
As a guideline, typical minimum requirements are given in H.2.1 to H.2.4.
NOTE Only design requirements are addressed in this annex.
D.1.2 | The responsible ATL shall review and adjust the requirements as required. |
D.1.3 | Checklists shall include an assessment of the condition of the equipment, as equipment in poor condition is likely to be unsafe. |
D.1.4 | A repairer shall either be a member of an approved mark scheme with a scope of repair including the type of product being repaired, or shall have the unit(s) being repaired batch tested by an ATL. |
D.2 | Requirements |
D.2.1 | Flameproof (Ex d) motors |
D.2.1.1 | All flameproof joints (including cable entries) shall be measured and shall comply with the required dimensions. This includes the dimensional requirements for joints interrupted by fastener holes. |
D.2.1.2 | All fasteners used on a flameproof enclosure shall meet the following requirements: |
(a) | the fasteners shall be metric; |
(b) | the fasteners shall not pass through the walls of a flameproof enclosure, unless they form a flameproof joint with the wall and are non-detachable from the enclosure; |
(c) | there shall be sufficient thickness of the material surrounding the hole, i.e.at least 1/3 of fastener diameter with a minimum of 3 mm (both parts); and |
(d) | the fastener holes on flameproof enclosures shall have the property class (for example, 3.6), or yield stress and type of fastener (for example, 180 MPa M12), marked. |
D.2.1.3 | Special fasteners are those connecting parts of the flameproof enclosure together and shall comply with fastener requirements and the following: |
(a) | the thread tolerance fit shall be 6g/6H (fastener/hole or male/female); |
(b) | the fastener heads shall be hexagon heads or hexagon socket set heads; |
(c) | the length of hole threads shall be at least equal to the major fastener diameter; |
(d) | the threaded hole shall have a thread tolerance class of 6H; |
(e) | the hole under fastener head shall have a clearance of ≤ H13; |
(f) | the hexagon socket set screws shall have a thread tolerance class 6h, and shall not protrude from the bottom of the threaded hole; and |
(g) | for Group 1 only,mechanical protection of the fastener head (for example, shrouding or counter boring) is required. |
D.2.1.4 | Cable entries shall meet flameproof joint requirements, and shall be marked with the thread size and type, for example, "½ NPT", "M25". |
D.2.1.5 | Aluminium frame motors shall not be used in Group I applications. |
D.2.1.6 | Interconnecting compartments shall be separated. |
D.2.1.7 | External fans and hoods shall be made of metal or anti-static plastic. This does not apply to Group II motors with a fan tip speed restricted to less than 50 m/s. |
D.2.1.8 | The minimum clearance between the fan and the hood shall be 1/100th of the fan diameter, ≥ 1mm, but need not exceed 5 mm. |
D.2.1.9 | An internal earth point in the terminal box and external bonding point shall be provided. |
D.2.2 | Non-incendive (Ex nA and Ex e motors) |
D.2.2.1 | The minimum rotor-stator clearance shall be checked and calculated. |
D.2.2.2 | The terminal box external IP rating (minimum IP54) shall be checked. |
D.2.2.3 | An adequate seal shall be in place between the terminal box and the winding compartment (if not, then the complete unit shall be IP54). |
D.2.2.4 | An approved gasket material shall be used on the terminal box. |
D.2.2.5 | The gasket shall be fixed to one side. |
D.2.2.6 | The terminal block shall be certified. |
D.2.2.7 | Overload protection shall be fitted to Ex e motors. |
D.2.2.8 | Aluminium frame motors shall not be used in Group I applications. |
D.2.2.9 | External fans and hoods shall be made of metal or anti-static plastic. This does not apply to Group II motors with a fan tip speed restricted to less than 50 m/s. |
D.2.2.10 | The minimum clearance between the fan and the hood shall be 1/100th of the fan diameter, ≥ 1mm, but need not exceed 5 mm. |
D.2.2.11 | An internal earth point in the terminal box and external bonding point shall be provided. |
D.2.3 | Ex tb and Ex tc motors |
D.2.3.1 | Metal or anti-static plastic fans shall be used, or the fan tip speed shall be s 52 m/s. |
D.2.3.2 | Light alloy contents shall not be, by mass, more than the following: |
(a) | for EPL Db (tb): 7,5 % in total of magnesium and titanium;or |
(b) | for EPL Dc (tc): there are no requirements except for fans. fan hoods and ventilating screens, which shall comply with the requirements for EPL Db. |
D.2.3.3 | Interlocking devices used to maintain the explosion protection (for example, thermistor loops for temperature limitation) shall require a proper tool to allow for adjustment or removal. |
D.2.3.4 | Terminal bushings shall be mounted in such a way that all parts are secured against turning. |
D.2.3.5 | Terminal compartments shall be dimensioned for |
(a) | sufficient space to readily allow connection of conductors, and |
(b) | to achieve any compulsory clearance and creepage distances. |
For LV cage induction motors, the minimum clearances and creepage distances given in table H.1, in accordance with SANS 1804-2, are required.
Table D.1 - Minimum clearances and creepage distances for LV cage induction motors
|
||||
1 |
2 |
3 |
4 |
5 |
Supply Voltage E
V |
Minimum Clearance mm |
Minimum creepage distance Mm |
||
Terminal assembly to metal parts |
Between terminal assemblies |
Terminal assembly to metal parts |
Between terminal assemblies |
|
E ≤ 250 |
2,5 |
2,5 |
3,0 |
3,0 |
250 < E ≤ 660 |
10,0 |
10,0 |
12,5 |
12,5 |
660 < E ≤ 1 100 |
14,0 |
16,0 |
18,0 |
20,0 |
D.2.3.6 | Internal earth point in the terminal box and external bonding point shall be provided. |
D.2.3.7 | For threaded holes for cable glands |
(a) | the thread type and size shall be identified, |
(b) | the thread type and size (for example, M25 or "½NPT") shall be marked on the equipment or shall appear in the installation instructions supplied by the manufacturer, and |
(c) | the holes with parallel threads shall have at least five threads, with a minimum tolerance of medium or fine. |
D.2.3.8 | The minimum clearance between the fan and the hood shall be 1/100th of the fan diameter, ≥ 1mm, but need not exceed 5 mm. |
D.2.3.9 | On large machines, equipotential bonding conductors should be fitted across enclosure joints, and symmetrically placed with respect to the axis of the shaft. |
D.2.3.10 | All joints in the structure of the enclosure, whether permanently closed or designed to be opened from time to time, shall fit closely together. They shall be effectively sealed against the ingress of dust, and shall meet an ingress protection of at least IP65. |
D.2.3.11 | The number of engaged threads for all threaded joints employing parallel threads, without an additional seal or gasket, shall be not less than five, with a minimum tolerance of medium or fine. |
D.2.3.12 | Gaskets under compression in joints may be used to ensure the effectiveness of the enclosure sealing. Gaskets and seals shall be of one-piece continuous construction, i.e. with an uninterrupted periphery. Gaskets shall be secured to one face of the mating surface, either by adhesive or mechanically secured;the design of the enclosure should be such that determination of the correct location of the gaskets can be made. |
D.2.3.13 | A sealant material (for example, silicone rubber) shall not be used on joints. |
D.2.3.14 | Cable glands shall be Ex t certified (preferably Ex tb). |
D.2.3.15 | The temperature rating shall be determined by a full load test without dust, including potential variations of ± 10 %. In addition, the maximum surface temperature may also be determined for a given depth of layer, specified by the manufacturer, which requires the motor to be marked with the symbol "X", to indicate this specific condition of use. |
D.2.4 | Ex i instruments |
D.2.4.1 | The integrity of safety components, safety separations and safety connections from certification documents shall be checked. If the certification documents are not available the circuit shall be assessed. |
D.2.4.2 | Electronic components shall be replaced with components of the same rating and tolerances. |
D.2.4.3 | The size of soldered joints shall not be increased, compared to the original. |
D.2.4.4 | Coatings that have been disturbed shall be restored to the original condition. |
D.2.4.5 | The IP rating shall be equal to, or better than, the original. |