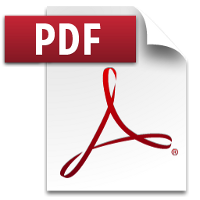
R
Occupational Health and Safety Act, 1993 (Act No. 85 of 1993)Code of PracticeDiving Regulations, 2009Code of Practice for Inshore Diving4. Operations4.1 Work planning |
Before any diving is carried out there must be a relevant dive plan available. The dive plan will consist of, at minimum, the diving contractor's standard Operations Manual and any appropriate site-and task specific risk assessments and procedures.
The dive plan must specify the diving equipment and techniques to be used as well as the requirements of the particular operation. It must specify contingency procedures for any reasonably foreseeable emergency.
Many factors need to be considered when preparing a dive plan for a diving project. The risk assessment must identify site-specific hazards and their risks. Based on this information, the plan will state how these hazards and risks will be controlled.
Whenever a diving project is planned, the information required in terms of the Diving Regulations must be forwarded to the provincial office of the Department of Labour in the prescribed manner.
4.1.1 | The Diving Project Plan |
The diving project plan defines the scope of diving work to be performed for a diving project and contains records of the conclusions, findings and decisions of the planning activities relevant to the project. It is both guidance for the dive team and evidence of due diligence by the Diving Contractor.
4.1.2 | The Dive Plan |
Dive plans contain the proposed profile and tasks of each dive and these are updated when required. The dive plan may refer to more detailed information in the diving project plan when appropriate.
4.1.2.1 | Quantity of gas |
The quantities of gases likely to be needed for diving operations, including for treatments and emergencies, must be calculated when planning a diving project. Allowances should be made for leakage, wastage, contingencies, etc. Diving must be stopped if the quantity of gas needed for safety purposes falls below the minimum specified in the operations manual and the dive plan.
A reserve supply of medical oxygen with a free volume of 40m3 is required at the chamber for the purposes of treatment in the chamber. A minimum supply of reserve air for the chamber is also required on site.
4.1.3 | HIRA (Hazard Identification and Risk Assessment) |
The dive planning for a diving operation is unique to that specific operation, and therefore only general guidelines can be given. The safe planning and implementation of the dive operation will be based on the Hazard Identification and Risk Assessment (HIRA) for that operation, in conjunction with the Diving Regulations, the contractor's Operations Manual and the task requirements.
4.1.3.1 | Requirement |
HIRA is required in terms of Regulation 22(1)
No diving operation is to take place without HIRA being carried out before the diving operation commences, and all relevant hazards identified and the associated risks assessed. The risk assessment will determine what diving mode is to be used and if diving is to take place at all.
The HIRA forms part of the project plan and the dive plans and is updated as required.
4.1.3.2 | Communication |
The results of the HIRA must be communicated to all dive team members and other stakeholders before the dive commences during a dive briefing or toolbox talks.
4.1.3.3 | Consultation |
The diving contractor shall carry out a HIRA and risk management process in consultation with the whole dive team and include inputs from third party specialists (e.g. Approved Inspection Authorities) when required by legislation or when otherwise considered appropriate
4.1.3.4 | Updates |
A comprehensive MIRA should be performed for each diving project, but provision should be made for an update prior to each dive. This process must allow for changes in the dive plan, based on the findings.
When performing the HIRA update, the diving supervisor shall consult with the other members of the dive team and include inputs from other persons whose activities may influence the health and safety of the divers.
4.1.3.5 | Records |
A copy of the relevant updated site and task specific HIRA documents must be kept as part of the diving operations records.
All of the findings of the HIRA shall be formally recorded including the names of the persons involved in the process. All of the aspects listed below should be included where appropriate. Records of health hazards should be kept in accordance with the Regulations pertaining to those hazards, e.g. Regulations for Hazardous Chemical Substances, Regulations for Hazardous Biological Agents, etc.
4.1.3.6 | HIRA Process |
The HIRA process shall:
• | identify and record significant hazards associated with the operation; |
• | ensure that an assessment is made to determine and record the risks associated with such identified hazards |
• | control such risks by implementing measures to either eliminate or reduce risks to an acceptable level. |
• | implement contingency and emergency plans and medical surveillance for risks that remain. |
4.1.3.6.1 | Hazard Identification process |
Health and safety hazards exist at all workplaces. A hazard is any agent. activity. situation or substance that can cause harm. Hazards can be divided into three groups, health hazards, safety hazards and hazards to the environment.
Existing and potential hazards shall be identified during the preparation of the Diving Project Plan and reviewed prior to the commencement of each diving operation. Any additional hazards which arise during the operation should immediately be brought to the attention of the supervisor and the operational plan adapted as necessary to ensure the health and safety of the workers, or the operation should be aborted.
4.1.3.6.1.1 | Health hazards |
An occupational health hazard is any agent that can cause illness to an individual. A health hazard may produce serious and immediate (acute) affects, or may cause long-term (chronic) problems.
Someone with an occupational illness may not recognise the symptoms immediately. For example, noise-induced hearing loss is often difficult for the affected individual to detect until it is well advanced.
Health hazards include: chemical hazards, biological hazards, physical hazards, psychosocial hazards and work design (ergonomic) hazards.
(a) | Chemical hazards: Chemical hazards include, but are not limited to: |
• | Breathing gases and the possibility of breathing contaminants |
• | Toxicity from gases breathed, e.g. nitrogen narcosis, oxygen toxicity, etc. |
• | Diving in chemically contaminated waters (e,g.harbours) |
• | Exposures to any dusts, fumes, vapours, metals, chemical irritants, pesticides and other chemical agents |
(b) | Biological hazards: Biological hazards include, but are not limited to: |
• | Risk of marine life injuries |
• | Diving in biologically contaminated waters |
• | Cross-contamination using diving gear |
• | Travel diseases like malaria or travellers? diarrhoea |
• | Exposures to viruses, bacteria in the workplace |
• | Any agent that can cause an infection in the diver |
(c) | Physical hazards: Physical hazards include but are not limited to: |
• | Radiation hazards |
• | Noise |
• | Temperature extremes |
• | Pressure (causing barotrauma, decompression sickness, etc.) |
• | Electrical shocks |
(d) | Psychosocial hazards: Psychosocial hazards include, but are not limited to: |
• | Working shifts (shift work) |
• | Diving in hazardous environments |
• | Involvement in stressful situations (eg. body recovery, mass casualties, etc.) |
(e) | Ergonomic hazards: Ergonomic hazards include, but are not limited to: |
• | lifting and bending with heavy equipment in and out of the water |
• | Abnormal postures |
• | Working with vibrating tools |
4.1.3.6.1.2 | Safety hazards |
A safety hazard is any agent which may cause i jury, or damage to property. An injury caused by a safety hazard is usually obvious. For example, a worker may be badly cut. Safety hazards cause harm when workplace controls are not adequate.
Some examples of safety hazards includes but are not limited to:
(a) | Environmental conditions: include, but are not limited to: |
• | physical conditions at the operations site and the sea states |
• | visibility |
• | cleanliness of the premises and plant |
(b) | Task related aspects: Include, but are not limited to: |
• | the use of explosives |
• | use of tools and equipment. |
(c) | Associated activity factors: Includes, but are not limited to: |
• | accessing the site (including emergency response) |
• | m other equipment at the site |
• | other structures at the site. |
• | Working alone |
• | Slipping/tripping hazards |
• | Fire hazards |
• | Moving parts of machinery, tools and equipment |
• | Work at height |
• | Pressure systems and dífferential pressure situations |
• | Vehicles |
• | Lifting operations |
• | Diving under, near ships, vessels, small craft, and boats - propellers, rudders, sea suction intake chests, etc. |
• | Live boating injuries |
• | Entrapment or entanglement |
• | Implementation of permit-to-work systems |
• | Lockout-procedures |
(d) | Emergency response factors: includes but are not limited to: |
• | location and availability of appropriate emergency systems and emergency response procedures. |
• | Unconscious diver recovery procedures |
• | Severely injured diver recovery procedures |
• | Availability of first aid kit and support |
4.1.3.6.1.3 | Environmental hazards |
An environmental hazard (hazard to the environment) is a release to the environment that may cause harm or deleterious effects. An environmental release may not be obvious.
For example, a worker who drains a glycol system and releases the liquid to a storm sewer may not be aware of the effect on the environment. Environmental hazards usually cause harm when controls and work procedures are not followed.
4.1.3.6.2 | Risk Assessment |
Risk Assessment evaluates the frequency, probability and the consequences of a hazard, into a semi-quantitative measure of risk.
The aims of a risk assessment are to:
• | Identify and evaluate risks to enable contingency planning and minimise potential risk to health, environment and equipment. |
• | Provide a baseline mechanism for communicating to operational personnel the risks and means of minimising them, of a particular task or project. |
• | Ensure staff compliance to the company health, safety and environmental requirements, as well as compliance with relevant statutory regulations, guidelines and contractual obligations. |
4.1.3.6.2.1 | Risk Assessment process |
The risk assessment shall be conducted in the following way:
(a) | Assess who may be exposed |
Exposure may take place during the dive or the person may be exposed while on the surface. The HIRA must include the health and safety of surface personnel also.
(b) | Assess how the persons will be exposed |
The exposure route may be important, for instance chemical exposures may be via the lungs or be absorbed through the skin. Skin exposure may cause local effect (eg. chemical burns) or may cause systemic effects due to absorption of the chemical
Mechanical injury (safety risks) may happen due to improper equipment being used or if a person is not familiar with the operation of the equipment or not experienced in its use
(c) | Assess the exposure "dose" |
The levels of the hazards are important factors to consider. (For example; The specific noise level can predict the level of hearing loss expected). The dose is estimated as a combination of severity and time of exposure.
In order to measure the levels of chemical substances, some physical hazard etc., the services of an Approved Inspection Authority ("Occupational/Industrial Hygienist") is required in terms of some of the Regulations.
Some exposures e.g. noise levels, cannot be measured under water.
(d) | Assess the exposure frequency |
The more often the person is exposed to the hazard, the higher the risk of injury or disease.
(e) | Assess the influences of exposures on each other |
Some exposures may have an influence on each other, for instance mixed chemical exposures. Exposure to any one of the elements may not be considered a health risk, but the combined effect of exposure may be considerable. Exposure to chemicals and noise may have a bigger effect in combination to any one of these in isolation. The assessment should thus take the 'big picture" into consideration.
(f) | Assess the consequences of exposure |
Some exposures cause acute effects while others may cause long4erm effects, like causing cancer, hearing loss, etc.
Consultation with the Designated Medical Practitioner and the Occupational Medicine Practitioner (or Occupational Medicine Specialist) is required.
(g) | Note all your findings |
All of the findings should be clearly noted in the HIRA. This will provide a record of systematic approaches taken to address risks and evidence of due diligence.
4.1.3.6.3 | Risk control |
Control of risk is achieved by selecting from the hierarchy of control measures one or more measures which individually or in combination achieve the required risk reduction. Only those hazards identified during the hazard identification process that pose a real (unacceptable) risk (as determined in the risk assessment process) need to be addressed. If the risk assessment determined that a hazard is associated with acceptable risk, this should be indicated in the HIRA and it need not be addressed further.
Where the level of risk cannot be controlled to an acceptable level, no diving work shall take place while the hazard is present.
Appropriate control measures shall be applied to the risks, using the hierarchy of controls in the following order:
(a) | Elimination |
In some cases risk may be eliminated by removing the hazard or operating when it is not present.
(b) | Substitution |
Where the risk can be controlled by performing the task using alternative methods, consideration shall be given to using these alternative methods.
(a) | Design |
Plant and procedures can be selected or designed to reduce risk.
(b) | Isolation |
Persons should be isolated from the identified hazards where practicable. Diving equipment can provide adequate protection from a number of hazards, e.g. hypothermia, marine stings, etc.
(c) | Administrative control measures |
Every operational plan should seek to minimize the degree and duration of the worker's exposure to risk. Rotation of workers is a good example to minimize exposure.
Almost every aspect of planning falls into this administrative category.
Administrative controls include, but are not limited to:
• | training, supervision, experience and selection of employees, including staffing levels; |
• | provision of an appropriate operations manual; |
• | organization and planning before, during and after the operation; |
• | selection of appropriate plant; and |
• | selection of the appropriate form and level of communication. |
(d) | Personal protective equipment |
Appropriately designed and sized personal protective equipment shall be provided, used and
maintained. The limitations of all equipment used shall be identified as part of the risk
assessment process. Information from manufacturers and from records of prior experience
should be used to identify Iimitations.
4.1.3.6.4 | Risk mitigation |
Risk is mitigated by planning or taking measures to reduce the effect of an incident associated with that risk on personnel, equipment and the environment.
These may include:
• | Emergency and contingency plans |
• | Provision of first aid and rescue equipment |
• | Retaining a DMP and/or recompression chamber on standby |
• | Spare tools and equipment |
4.1.3.6.5 | Recording of occupational exposures and medical surveillance |
If the HIRA process is followed and risk mitigation strategies are put in place, there will still be a level of risk that is accepted as part of the operation. In case any employee is exposed to such a risk that remains, appropriate measures shall be put in place to specifically screen such an employee for consequences of the exposure (including the levels of exposure, e.g. using Biological Exposure Indices) and the possibility of an occupational disease.
Screening for occupational diseases shall be conducted in consultation with an occupational medicine specialist, occupational medicine practitioner or an occupational health practitioner (as appropriate).
An accurate record should be available in the diver's medical file. This is a requirement in addition to the normal "fitness to dive's evaluation of divers.
4.1.4 | Diving mode |
Diving mode is selected for the operation based on the requirements of the specific task and the logistics of the operation, based on the indications of the HIRA.
Three modes of diving are possible under this Code:
4.1.4.1 | Surface supplied diving |
This is the default mode and is applicable to the full scope of diving activities covered by this Code.
4.1.4.2 Scuba diving
This may be used for activities which are not proscribed for scuba, provided that the HIRA indicates an acceptable level of risk, and provided that the procedures are authorised in the company Operations Manual for the applicable circumstances.
Scuba equipment is specified in section 5.2.2
Scuba has inherent limitations and difficulties such as limited breathing gas supply, last diver, etc. and scuba should therefore not be used if surface supplied equipment is available and its use is reasonably practicable.
Whenever scuba diving is performed, life lines (tended by competent diverse tenders), buddy lines surface markers and emergency gas supplies (bailout sets must be used as reasonably practicable, and provided they do not increase overall risk. The divers should be tethered to the surface marker with an 8mm diameter synthetic line (or equivalent) and this must be constantly visually monitored from a location that allows immediate assistance to be rendered in case of an emergency.
If the diving contractor, the diver and the diving supervisor all considers the use of one or more of these hazardous, then alternative measures shall be put in place to ensure that:
• | Voice communications between the divers and the diving supervisor is issued; and |
• | A buddy system is employed whereby two divers remain at all times in constant visual or physical contact and that both end the dive immediately if contact is lost; and |
• | The diver can be easily located by his fellow divers; and |
• | The diver can be located without any difficulty by the standby diver; and |
• | The diver can be rescued without any delay or difficulty in case of an emergency |
• | A lifeline is used for the standby diver. |
4.1.4.2.1 | Proscribed activities for Scuba diving |
Scuba may not be used at construction or industrial diving operations that involve the following:
welding, burning/cutting, high-pressure jetting, hoisting, dredging, using power tools, or working in an environment contaminated by hazardous materials or microorganisms.
Scuba may not be used for penetration of overhead environments where the exit cannot be clearly seen by the diver under all reasonably foreseeable circumstances.
4.1.4.3 Airline diving
This may be used for activities which are not proscribed for airline, provided that the HIRA indicates an acceptable level of risk, and provided that the procedures are authorised in the company Operations Manual for the applicable circumstances.
Airline equipment is specified in section 5.2.3.
Use of airline equipment may be considered when:
• | The risk of diver entrapment is low, |
• | The risk of snagging the airline is low (in most applications the risk of snagging the airline is minimised by use of a buoyant airline which is sufficiently strong to serve as the lifeline, |
• | Full surface supply equipment is not appropriate for economic or logistical reasons, |
• | no proscribed work required, |
• | Airline mode is required or recommended by a government department for the specific industry. |
A bailout system must be carried by the diver when there is any significant risk of the diver being unable to make an immediate, direct and acceptably safe ascent to the surface and to immediately achieve positive buoyancy in the case of a failure of primary air supply. Any ditching of equipment required for such a free ascent may not involve more than one quick release buckle, operable by either hand in a single movement, and all equipment required to fall clear must do so in any reasonably foreseeable circumstance, A bailout system must be used if obligatory decompression is a plausible contingency.
The standby diver may be equipped with any mode of diving equipment permitted by this Code and acceptable in terms of the HIRA. The standby diver should use a lifeline if on Scuba unless the HIRA shows this to be impracticable or it increases the risk.
A line attendant must be used in all operations where airline diving is used. The line attended must be competent and have the relevant knowledge of line signals to be used during the operation.
4.1.4.3.1 | Proscribed activities for Airline diving |
Airline diving may not be used at construction or industrial diving operations that involve the following: welding, burning/cutting, high-pressure jetting, hoisting, dredging, using power tools, or working in an environment contaminated by chemicals, hazardous materials or microorganisms. Nor may it be used in circumstances where a differential pressure environment exists (e.g. dams, dry-dock locks, in the presence of valves, etc.). Diving depths exceeding 15m, or where the no-decompression-stop limits are likely to be exceeded.
4.1.4.3.2 | Permitted activities for Airline diving |
Airline diving may be stipulated by a government department for some applications.